The principle and phenomenon of thermal warpage of connector reflow soldering
Most people do not understand the principle of thermal warpage of connector reflow soldering. The Lilutong waterproof connector manufacturer with 20 years of manufacturing experience will explain the principle and phenomenon of thermal warpage of connector reflow soldering for you.
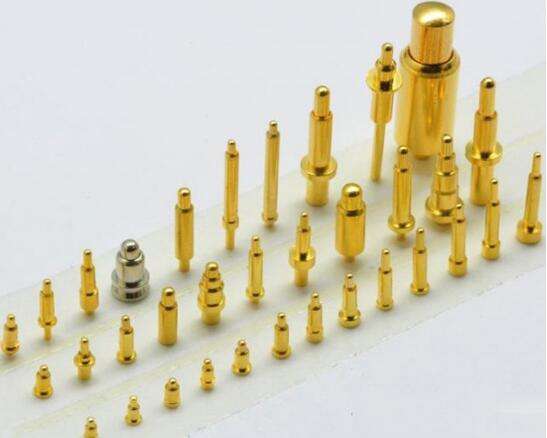
The main reason for connector reflow soldering is: uneven shrinkage. The reasons for the change in shrinkage include: uneven temperature inside the plastic part. When the plastic part is solidified, the pressure difference and cooling rate difference along the thickness direction. The plastic part is ejected before it is completely cooled, or the ejector pin is deformed, the barb is too deep, the ejection method is improper, and the ejection angle is improper, and other factors may cause the plastic part to warp. The change in the thickness of the plastic part leads to the difference in the cooling rate. Plastic parts have curved or asymmetrical geometric shapes. There is no difference between the material of the plastic parts and the filler. The flow direction and the molecular chain perpendicular to the flow direction, the difference in fiber orientation, the difference in the packing pressure (for example, excessive packing at the gate, insufficient packing at the place far from the gate).
The main causes of reflow thermal warpage are residual stress after injection molding, anisotropic thermal expansion of materials, and thermoplastic deformation. After the connector is injection molded, during the cooling process, the outside shrinks, but the inside still maintains a high temperature, and the shrinking is slower than the outside. After cooling, the inside and outside of the connector will be subjected to self-tension and compression stress. Some of these stresses will form warpage, and some will remain in the connector as residual stress. When the connector goes through the reflow process, the residual stress will be released, causing the reflow thermal warpage. After the connector is injection molded, its material is anisotropic in thermal expansion. Therefore, after the thermal field of a reflow process, uneven thermal expansion and contraction will be formed, which will eventually cause thermal warpage and deformation of the connector.