Three factors leading to the failure of automotive connectors
Cars are the most common means of transportation in our daily lives, and safety is always the first choice people give priority to car product quality. Therefore, automobile manufacturers pay particular attention to the safety and quality of their products. As we all know, a molded car is made up of many kinds of parts, which means that car manufacturers have very strict requirements on suppliers of these parts.
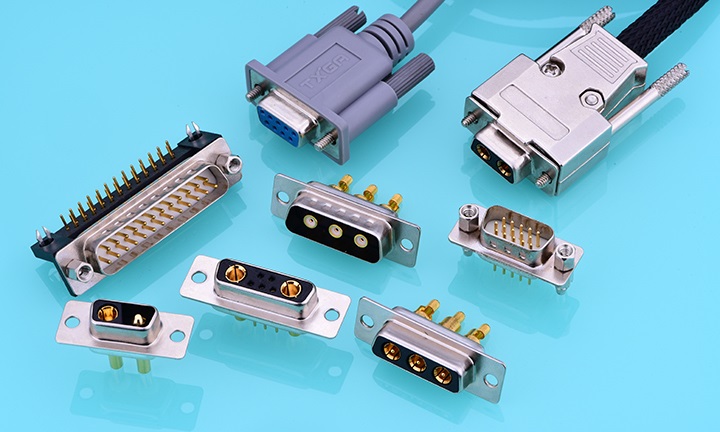
Take the car connector, an ordinary car has more than 1,000 connection points, of which more than half of the connection points are used for key power distribution functions, plus car connectors are often exposed to increasingly harsh environments Within, for example, under the effects of temperature, operating vibration, friction corrosion and oxidation, the selection of performance and stability of automotive connector products by automobile manufacturers is extremely important.
In fact, the selection of connector suppliers by automobile manufacturers is not as simple as imagined. There are also many cases of serious consequences caused by automobile operation due to failure of electronic connector components. Therefore, whether it is an automobile manufacturer or a connector supplier, it is necessary to analyze the knowledge points of the physical or mechanical phenomena that may affect the performance of the connector in the environment.
In order to evaluate the stability of the connector, some connector manufacturers have specially implemented elaborate test procedures. If the car connector fails, most of the common conditions can be determined as one of the following three factors, such as: connector friction corrosion , Connector electrical failure and connector plugging problems, etc.
1. Connector plugging problem
When installing wiring in a car in a manufacturing assembly plant, improper connection of the car connector may cause the connector product to malfunction. To overcome this problem, electronic component design engineers often develop various connector locking devices. Another way is to use a plug-in auxiliary device to simplify the plug-in process of larger connector products.
2. Connector friction corrosion
Corrosive gases, high humidity and strong oscillation are the causes of oxidation and frictional corrosion of electronic components, and the three major conditions that lead to the failure of automotive connectors. These environmental factors will have a great impact on the contact surface of tin and lead-tin, which is the case for 90% of the surface of electronic connectors.
3. connector electrical failure
The connection problem of the cable and the terminal is one of the main reasons for the failure of the warranty and automobile connector system. For automotive wiring systems, crimping is a very common method for connecting terminals to cables. This process has been proven reliable. Compared with the welding method, it is more economical and simple to operate in terms of improving crimp reliability.